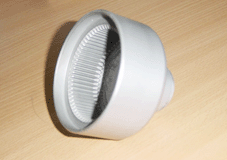
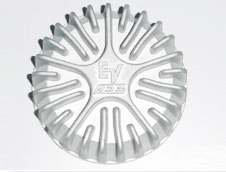
What is the Difference Between Casting & Forging?
Casting and forging are popular metal forming processes used to create parts and components for a variety of industries. However, these processes are very different from each other, and yield products with varying characteristics. As a leading outsourcing authority for metal forming and fabrication, we’re here to clarify what distinguishes casting and forging from each other, and help you decide which is better suited to your project’s requirements. Let’s begin by breaking down the definitions of each.
What is Forging?
Forging uses dies, pressure, and temperature to shape a solid piece of round metal bar into a shape. There are three ways forging can be classified: 1) temperature (hot, warm, or cold forging), 2) type of process (open or closed die forging), or 3) material used (steel forging, aluminum forging, brass forging, or bronze forging).
What is Casting?
Casting is the process in which molten metal is poured into a hollow cavity mold and later cooled to form a solidified part. Types of casting vary based on the molding materials, casting process, and filling pressures. Die casting, investment casting, permanent mold casting, and sand casting are the main metal casting methods.
Forged vs Cast
To summarize, castings are melted, poured, and solidified, while forgings are physically forced into a shape while remaining in a solid state. As a result, these two processes form end products with very different characteristics. When deciding which process is best suited to your project, it’s important to narrow down your priorities. Is it a complex shape? Is it large in size? Does it require high levels of strength? Refer to the chart below for the most common considerations to keep in mind when choosing between casting and forging.
Factors to Consider When Choosing Between Casting & Forging
|
Metal Forging |
Metal Casting |
Structural Integrity |
Far superior in strength compared to castings. High level of material predictability |
Products tend to be more porous and more susceptible to breakage compared to forgings |
Tolerance |
Not well suited to highly complex geometries |
Allows for a high level of detail. Able to adhere to tight tolerances |
Product Size |
Limited in terms of the size and thickness of the metal (larger = more difficult) |
Compatible with a wide range of sizes |
Material Selection |
Selection of alloys is limited |
Compatible with nearly all types of metal |
Secondary Operations |
Usually requires secondary operations to refine and finish product to exact specifications |
Provides primary product that will usually require very few secondary operations |
Cost |
Tends to be most cost effective for medium to large production runs |
Generally, less expensive compared to forging, but it depends on the specific casting method used. |
Grain Flow as a Factor
Grain flow is at the center of what separates these processes from each other. In forging, the metal is pounded and deformed, but the grain flow remains unbroken, allowing it to retain its strength. In casting, the metal is melted down, which breaks the grain flow and causes the metal to lose some of its initial strength once it solidifies. As a result, forged metal is less likely to shatter than cast metal.
Which is Better, Casting or Forging?
All in all, casting tends to be the less expensive, more versatile option, however; forging offers superior strength and wear resistance. The question of which is better depends on the top priorities for your project. If low cost, exotic alloys, and complex geometries are a priority, casting would probably be the way to go. However, if strength and structural integrity are concerned, forging may be the better option.
Explore examples of our past work to see what Compass & Anvil’s metal forging sourcing services can do for you and your planned project.
Discuss Your Forging or Casting Needs with Compass & Anvil
With over 30 years of industry experience, Compass & Anvil is an expert on castings and forgings. As a leading outsourcing authority, we can find a domestic or international manufacturer to take care of all your metal forming needs. We provide hands-on facilitation from initial design all the way through fulfillment to ensure you receive the high quality products you need. Backed by our quality guarantee, we can make certain the parts you receive match your exact specifications, or your money back. Contact us today for a free, no obligation consultation.
Contact us today at (408) 205-1319 (Pacific Time) or email us for a no obligation quote or to request additional information about forging vs. casting processes.